Another Ranger Boats Product Knowledge Tour has come and gone (December 6, 2004) and I believe they’ve outdone themselves – more changes than any other year since I began going to the Flippin, Arkansas complex.
Building a Quality Bass Boat Pages
December 2004 Factory Tour Update
Of course, there’s no question much of the buzz is about the new Ranger Z-Comanche Series boats – 18 months in secret development with a dramatic release at the 2004 FLW Tour championship. Quite a bit of this year’s product knowledge tour centered on the new Z-Comanche Series. Four of us traveled to Flippin to test drive the new Z series boats, which we did on a cold, rainy Saturday. Good thing I brought my rain suit… but rain or no rain, what a ride!
Regardless of whether you’re a Ranger Boats owner or not, I think it’s valuable to know how these fishing machines are made. There are common issues in purchasing and owning a fishing boat regardless of brand – helpful things to know when you buy your next boat.
If you’ve never had the opportunity to visit a boat factory, you may find some of this information and the pictures interesting and I hope informative. I’m unabashedly a Ranger Boats fan. I think you’ll understand why once you’ve read these pages.
I’m not trying to convince you that Ranger Boats are the only worthy boats out there, but personally, I feel a purchase this significant should be made with as much knowledge of the product as possible. Are you getting your money’s worth?
Especially if you plan on running the Great Lakes and other BIG waters. No matter what brand you are looking at, it’s helpful to you to know to ask your dealer things like what is in the transom in this boat?
You want to know it will hold up. Or is this boat ‘hand-laid’ and what exactly does that mean? And even asking what controls were in place to ensure continuity and consistency in fiberglass/resin application? These are just a few very important things to think about when making the major investment in a bass boat.
This being my 4th product knowledge tour (2000, 2002, 2003, 2004) now in 5 years, I can say that I’m impressed by the number and quality of changes that occur every year at Ranger Boats. A sign of a good company is a constant drive to improve processes, materials, safety and impact on the environment. This year I witnessed more of this drive than ever at Ranger. It’s probably very good for the industry that one of the leaders isn’t just sitting back on its laurels.
Ranger has its broadest range and style of fishing and family boats yet. All these new boats and styles, along with constant improvement make for an interesting tour.
The factory complex is large and Ranger Boats is known for making most of their components in-house, which provides a thorough tour of the complete process of building a quality fishing boat and all that goes with it. If you are the kind of person who likes to know what makes things tick, I think you’ll enjoy this virtual tour.
Note
If you’d like to take your own factory tour sometime, Ranger Boats gives free tours frequently. Find out more by clicking this tour info link. The large factory knowledge tours no longer exist.
J.D. Power has rated Ranger Boats Number One three years in a row – 2001, 2002 and 2003.
The Hull and Cap – Molds
Gelcoat / Fiberglass Application
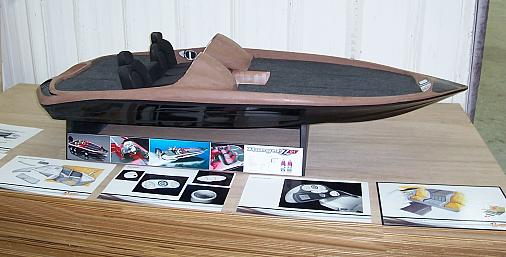
In an entirely new model first comes the concept. The concept goes through many steps including engineers and artists. In the case of the new Z-Comanche series project, months of design work leading to this 4-foot clay concept model. Every surface is digitally recorded for further testing and study. The digital images can be used to create the first fiberglass or wooden plug, or sent to the Genmar VEC plant in Pennsylvania for the unique VEC one-piece production.
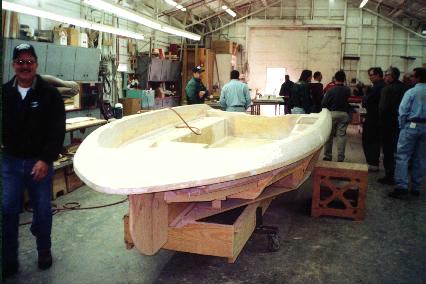
All molds begin with the wooden or fiberglass plug crafted inside the R & D shop. Craftsmen hand-design the plug. Test boats are made from molds of the plug. A final plug is selected after extensive testing of the hull. A matching interior deck design is chosen (such as this deck plug here). All molds used in production come from these plugs or masters (wood plugs are reproduced in fiberglass later) after they are polished to a high gloss level and treated with a release agent.
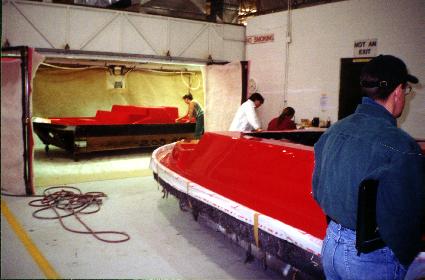
Properly prepped molds are critical for producing a high gloss gelcoat on the deck and hull part. This prevents unnecessary buffing of the hull or deck later. Gloss levels are measured electronically to meet standards. Molds, such as these 500 series deck molds, are repolished chemically and manually after a certain number of units (or if it falls below standards) by mold maintenance teams.
Release agents are used to separate the parts without damaging the mold or unit once the part has cured the correct amount of time.
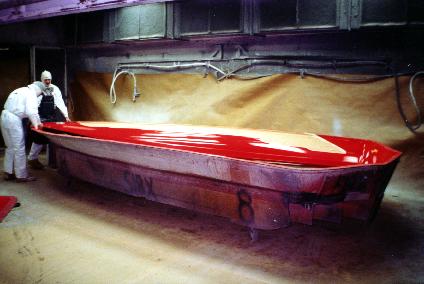
All the stripes are hand-taped by trained technicians. I don’t know how they do it so well so often, but they do. Tape is removed from stripes as each new layer/color of gelcoat is sprayed.
Mold maintenance is critical to the success of the part. The high gloss finish depends on the quality of the mold. The depth of finish is monitored constantly for each part. Each mold is numbered and parts are tracked so if any issue is identified with a mold later, all the parts produced from that mold can be pulled back and reviewed. There may be 100 molds in use at a time with several molds for each model.
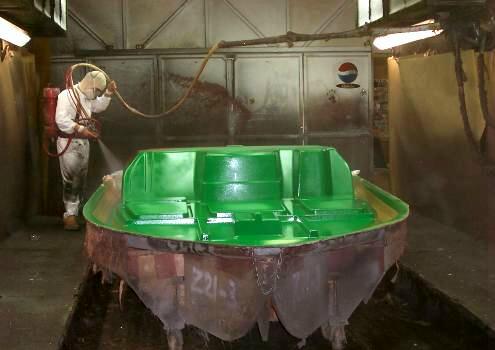
Gelcoat application is done in booths with new and improved ventilation that along with better materials has greatly reduced impact on the environment. Boats take up to 30 separate spraying steps. This is where the main difference between R/Sport-Series and Comanche boats occurs. R/Sport-Series boats are made using all the same materials and processes, but their pre-set color schemes, require less application steps than the more complex striping and color schemes of Comanche Series boats.
After each layer of top quality ISO-NPG gelcoat is applied, an opaque back-up layer is sprayed to protect from bleed-through and give poly finishes depth. Thickness is continually monitored.
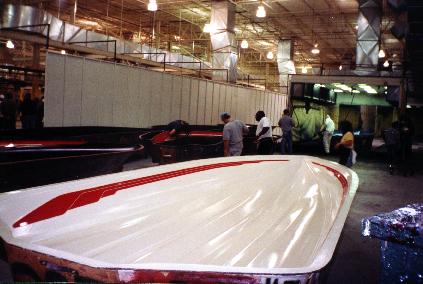
Pinstripes and Panels are untaped in the order their colors are applied after each gelcoat & back-up layer cures. Styles lines in the molds aid in taping and add attractiveness and strength to the resulting part. The new spray canister process shown above also has reduced waste and improved gelcoat/flake application.
Almost 60 different colors are available in solid, polyflake and polymist varieties. Polymist is a new option with tiny colored flakes verses the large flakes in Polyflake. I really like the new Polymist. All these gelcoat layers protect against water damage to the fiberglass layers applied next.
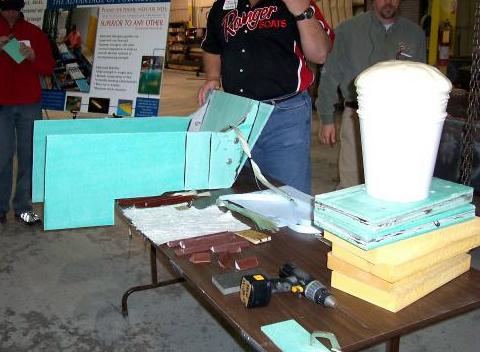
What’s in your transom? Many fiberglass types go into making a bass boat. Different types for different areas of the boat. They included Ranger’s exclusive, patented pultruded, woven-roven, multi-axial and fiberglass ropes of various thickness and strengths. High stress areas such as the running pad, transom and hull bottom, and deck corners receive hand-laid fiberglass reinforcement – up to nine layers.
Extremely strong fiberglass rope is placed in each hull strake during lamination providing exceptional longitudinal strength similar to re-bars in concrete. Some manufacturers fill hull strakes with putty-like materials that offer little if any additional strength.
The putty triangle samples on the table used by some boat builders were broken into small strips easily by hand. The fiberglass rope Ranger puts in their strakes would not break even when repeatedly rapped hard on the table edge.
The exclusive pultruded fiberglass transom and gusset assembly used in all Ranger boats is three inches thick and stronger than steel pound-for-pound in compressibility and sheer strength. Aluminum corners and an aluminum layer inside the transom section complete the assembly. This whole assembly will be glassed into the hull of the boat.
Some bass boat manufacturers use composite sheets of about the same thickness in their transoms. They are essentially a high-density foam-like material. You can wallow out the boltholes by hand in just a few seconds in these composite blocks. You can’t do that with the pultruded fiberglass sheets. They do a demonstration of this by placing the Ranger transom section over a large metal bolt. By twisting the Ranger pultrusion assembly, they easily bend the heavy bolt without changing the bolt hole in the ultra dense fiberglass.
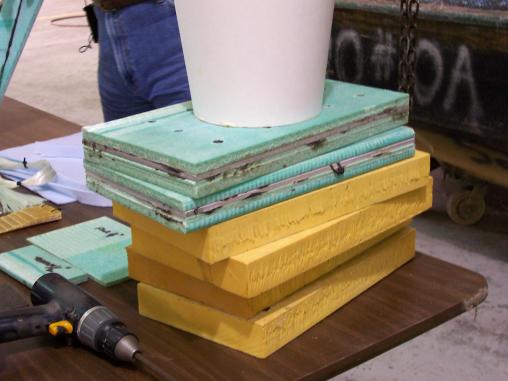
The composite section other builders use can’t bend the bolt, but actually wallow out the bolt hole creating a loose fit. This makes it clear that keeping outboard bolts tight always is critical for hull and motor mount integrity in a composite hull. Any play could quickly cause dangerous transom damage creating a situation where tightness may not be able to be maintained.
The stack above shows two sections of a Ranger transom verses several sections of composite. The pultruded fiberglass sheets Ranger uses have to be cut with a 55,000-psi water saw. I know what I’d rather have in my transom when I’m looking out across Lake Erie.
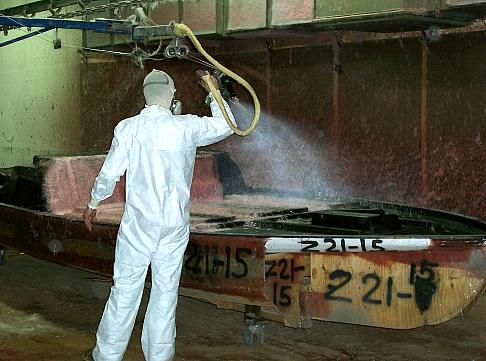
High stress areas are reinforced with hand-laid multi-axial fiberglass cloth along with areas of sharp radii to make sure no air pockets form, strengthen the gelcoat finish and ensure a strong bond between the gelcoat and fiberglass dramatically increasing the durability of the part. Then a first layer of fiberglass is applied with a chopper gun. The chopped fiberglass goes on in multiple directions using a measured amount of resin. Strength is in the fiberglass, not the resin so consistency of the fiberglass to resin ratio is important. Thickness is checked in several areas to guarantee adequate reinforcement.
You hear manufacturers claiming their boats are hand-laid in way that makes it sound like the best way to build a boat. This is misleading in several ways. Often, a claim of hand-laid truthfully only applies to part of the boat, usually just the hull or part of the hull. It’s actually much more difficult to hand-lay the cap with all it corners and turns.
Consistency is critical to a strong part, especially boat after boat. Hand-laid parts introduce a potential for error such as too much resin for the amount of fiberglass or especially difficult, controlling the smooth bonding and curing of resin and fiberglass along the entire part. An edge or weakness in the hull or deck can occur where sections of hand-laid glass didn’t cure together smoothly. You only have a short window of time to work with the resin.
The chopper gun works better for the large parts such as the hull and cap because it can be applied quickly and consistently even into sharp corners and contours. Ranger uses proper controls to ensure a good result. Chopper gun applicators are trained 8 months to do the job consistently. The fiberglass is weighed as it is applied to guarantee the proper and consistent amount is used for the various models.
The high-tech equipment Ranger uses not only weighs the fiberglass, but also measures the proper amount of resin to maintain a uniform ratio of high fiberglass to resin for a stronger part. A consistent single unit part is created. Excess resin adds unnecessary weight. The chopper gun equipment prevents that.
Some companies produce boats with up to 70% resin. This is excess weight, not strength. Ranger’s partial hand-laid and multi-directional chopper gun process provides a strong consistent 60 – 40 ratio. The pultruded reinforced transom and backing is an incredibly high 75% fiberglass to 25% resin.
Combining the proper types of reinforcing fiberglass materials in the right areas, then adding the efficiently and evenly applied chopped fiberglass in a high fiberglass to resin ratio is one of the main reasons why Ranger Boats are built to last, and why I feel much safer when I’m forced to ‘surf’ the huge waves of the Great Lakes. Unless you’ve ever fished were you could not see shore in any direction, you have no idea how truly critical it is to be riding in a boat you have the ultimate confidence in!
Another significant key to a strong, long-lasting hull and deck is cure time-length. Ranger usually has over 100 boats on the floor at any one time. To do so, they need several molds for each model since they leave each new hull and deck in the mold for 3 full days to cure before the hull is removed and sent to rigging. Other boat companies use less molds so they only cure their parts one day. Hull and deck consistency is assured because each mold comes off of the same master plug.
I cover this topic so much because there is quite a bit of misleading information out in the market that does nothing for us anglers except add confusion. And I believe information makes all of us smarter consumers and hopefully safer boaters.
I hope you've found this information interesting, educational and informative. Please use the link below to get to page 2 for more pictures and info on hull and deck finishing and lamination from my visit to the Ranger Boats factory.